Corrective and Preventive Actions (CAPA) are quality management processes that help organizations deliver a high-quality and error-free product.
Today’s post will provide details of these two quality management processes, with examples, templates, and an action plan.
Corrective and Preventive Action (CAPA): Definition & Meaning
Definition & Meaning: Corrective and preventive actions (CAPA) involve two processes: “corrective action” and “preventive actions.”
Let’s start with the first one.
Corrective Action
Corrective actions remove the cause of nonconformity from a process. It is a reactive process. Here, an error has occurred, and it ensures that the error will not happen again.
According to ISO 9001, “The organization shall take action to eliminate the causes of nonconformities in order to prevent a recurrence.”
Preventive Action
Preventive actions help stop nonconformity from a product or process before it occurs. It is based on experience or lessons learned. Preventive action is a proactive process that ensures that the product and processes are error-free.
According to ISO 9001, “The organization shall determine an action to eliminate the causes of potential nonconformities in order to prevent their occurrence.”
Examples of Corrective and Preventive Action (CAPA)
You have identified a dimensional error in your deliverable. You replace the deliverable and change the equipment settings, so the deliverable is of the exact dimension, and the error does not occur again.
This is an example of corrective action. The error has occurred, and you took measures to ensure that this error does not happen again.
Now, let’s see an example of preventive action.
You join an organization and are going to start a new process. The new process will use equipment that you have used in the past.
With the previous organization, you have identified an error in the equipment and are afraid it may happen with the current equipment. So, you check the settings and ensure that the error will not occur now.
This is an example of preventive action because the error has not yet occurred, but you took measures to stop it.
For certain industries, CAPA is a legal quality management requirement in some countries. For example, in the USA, pharmaceutical companies must follow CAPA compliance.
Failing not to follow the CAPA can lead to pharmaceutical products as adulterated.
It is an FDA (Food and Drug Administration) requirement in the USA to have a CAPA process.
Corrective Action Vs Preventive Action
The following table shows the difference between corrective and preventive action.

Corrective Action Vs Correction
Correction is another quality term, also known as defect repair. In correction, nonconformity occurs, and you must correct or replace the deliverable.
If the nonconformity is repairable and the repair cost is less than the deliverable cost, you will repair it; otherwise, you will replace the deliverable.
Also, if the deliverable is not repairable, you will replace it regardless of the cost.
Corrective and Preventive Action Plan
According to ISO 9001, implementing CAPA requires seven steps.
- Define the Problem: Identify the problem, whether it is a process issue or a problem with a deliverable. The problem should be real, not a perceived one.
- Define the Scope: Understand the context, and the issue, analyze the problem and find its root cause and impact on other processes.
- Containment Actions: Take immediate measures to stop it from occurring and then develop a thorough plan to contain the error and stop the issue permanently.
- Identify the Root Cause: You must identify the root cause of the problem. You can use a fishbone diagram, five whys, etc.
- Plan the Action: Develop a realistic plan with realistic deadlines and solve the root cause of the issue. You can use cost-benefit analysis if the issue is big and requires a large investment.
- Take Action: Implement the plan to contain the nonconformity.
- Follow-up and Ensure the Plan Worked: Review the plan and see if it was successful.
CAPA Template
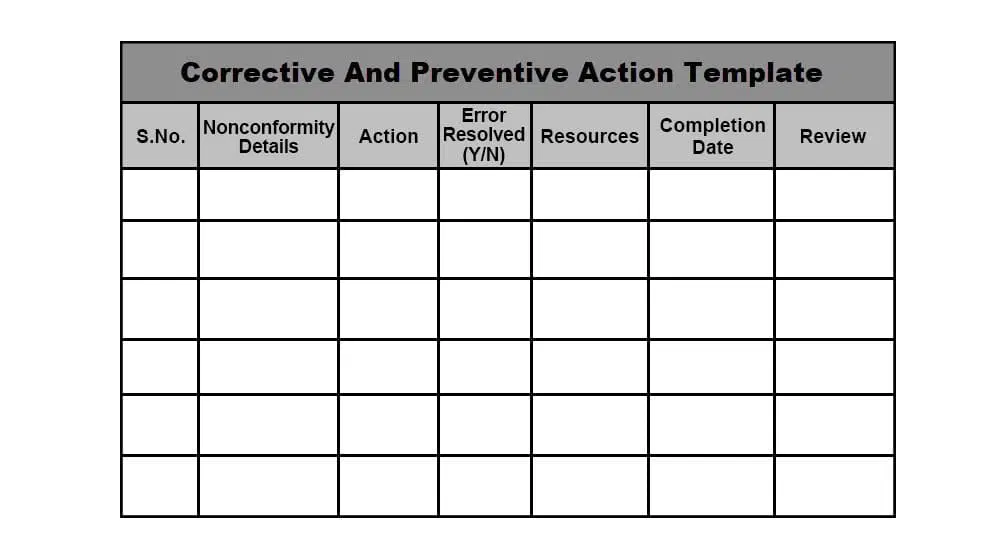
Summary
Corrective and preventive actions (CAPA) require the same activities; however, the trigger is different in both cases. In corrective action, a nonconformity has occurred, and you must take corrective measures to correct the process to stop it from happening again.
On the other hand, preventive action is a response to an anticipated error that has not occurred but taking measures so it will not happen.

I am Mohammad Fahad Usmani, B.E. PMP, PMI-RMP. I have been blogging on project management topics since 2011. To date, thousands of professionals have passed the PMP exam using my resources.
It’s nice that you pointed out how corrective actions would remove the cause of nonconformity from a product. I was reading management guide last night and I learned a small bit about CAPA. From what I gathered, it seems there is corrective action software now too.