Calculating a Bill of Materials (BOM) is a key process in project management and manufacturing industries. A BOM is also known as an assembly ingredient list, a product structure, a bill of quantity, a product blueprint, etc.
BOM is also useful in supply chain procedures. For example, materials requirement planning, stock management, forecasting, product pricing, etc.
What is a Bill of Materials (BOM)?
Definition: A Bill of Materials (BOM) is an organized list of the materials, consumables, elements, and accessories required to complete the project or produce or repair a product. The price and quantity of such are other key elements.
A BOM can include instructions on using these items. It can serve as a central repository for the project and its production materials. In production, it works as a schedule for a particular product and includes all ingredients, parts, and procedures.
Most BOMs consist of a hierarchical structure. The final product is at the top, followed by sub-assemblies. It includes parts names, numbers, descriptions, and quantities.
Although the BOM is a simple concept, it can be challenging to create it if the product includes several different items.
A delay in component delivery can affect the schedule across the entire BOM, wherever this component is used. Adhesives are one example of a simple element that has various uses.
What is Included in a Bill of Materials?
The main components of BOM are the following:
- BOM Level: This number shows where the item falls in the BOM hierarchy.
- Part Number: Manufacturers assign part numbers to equipment spares. This one number helps identify an item and its specification. Users don’t have to check the complete specification. The part number can include numbers and letters. Being consistent is important.
- Part Name: The part name serves as a distinctive identification. It aids users in identifying the part, just like the part number.
- Phase: It shows the part’s so-called lifespan stage, such as “in-production “or” in-design,” for instance.
- Description: The description is exclusive to the specific part or component and offers more detailed information on the part, unlike the part name or number. To distinguish between pieces that seem identical, descriptions come in handy. For instance, “screws” might refer to a specific type of screws, such as machine screws that are 1/2- and 5/8 inches long.
- Quantity: The number of components utilized in an assembly. A good illustration would be a piston cylinder with two piston rings.
- Metric Units: This specifies the unit of measurement used when buying and/or using a component. The proper amounts are ordered when the measure is specified. For instance, you buy wire in meters. Cheaper items may be acquired by weight or by the box.
- Type of Procurement: This details the method of obtaining the part or component. Options include buying the component using cash, PO, supply agreement, consignment, etc.
- Referential Identifier: The reference designator is used when printed circuit-board assemblies are present in a product. The circuit board assembly’s reference designator indicates each component’s specific placement.
- Notes for the Bill of Materials: You can add additional details in the BOM’s notes area. For example, you might want to include backup vendors or the requirements a substance fulfills, such as an adhesive.
Note that the labor is not included in the bill of materials.
The Structure of the Bill of Materials
You may use one of the following techniques to organize BOMs:
#1. Single-Level Bill of Materials
Each component used in the product is listed once in a single-level BOM, along with the required amount. It is like a grocery list.
Single-level BOMs are simple but do not show the connections between the assemblies, sub-assemblies, and components utilized to make a product. As a result, it can be challenging to pinpoint precisely which part of a product needs to be fixed or replaced if the system malfunctions.
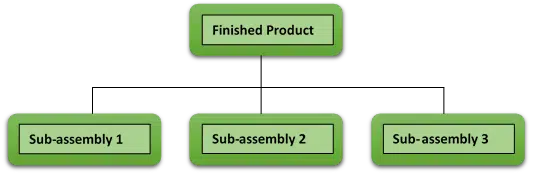
#2. Multi-Level Bill of Materials
A multi-level BOM shows the relationship between elements and sub-elements. It is sometimes knowns as parent-child. Here, you indent the components and sub-assemblies that make up the higher-level assembly. Multi-level BOMs are hence sometimes referred to as indented BOMs.
A sub-assembly may consist of many components. A modification in the assembly (or parent) propagates down to the sub-assembly (or child).
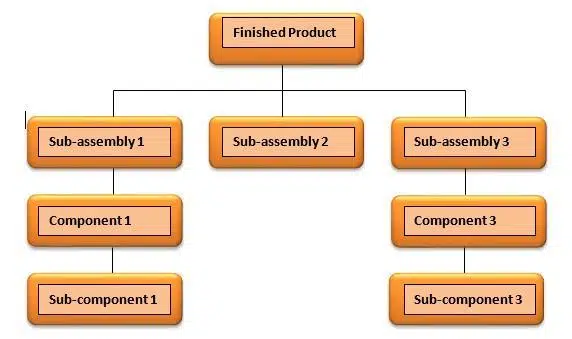
Different Types of Bill of Materials
For usage at various phases of the product development lifecycle, single and multi-level bills of materials may be developed.
The three main categories are BOMs are engineering, sales, and production.
Engineering Bill of Materials (EBOM)
A product’s initial design is specified in an engineering BOM. It includes the pieces, components, sub-assemblies, and objects defined by engineering. A technical sketch of the product often makes up this document.
As their name suggests, engineering BOMs are often created by engineers. They frequently utilize CAD software or other equivalent programs to produce the BOM.
Sales Bill of Materials (SBOM)
Sales BOM describes the materials needed to create a product. It is created using the sales order and contains the final product and its components.
Manufacturing Bill of Materials (MBOM)
A manufacturing BOM is used during production. It lists the components and assemblies, including packaging, required to make a shippable product and considers waste and materials used during the manufacturing process.
An MBOM outlines the work required on product components and groups the parts required at each manufacturing stage. This aids the people involved in figuring out when various production processes must commence and when supplies must be received in time to satisfy any delivery deadlines.
An MBOM for a new product could be in effect for a predetermined time frame, such as a few weeks. The MBOM can then be modified, or a new one may be developed if the product requires improvements to be made.
The enterprise resource planning system and material requirement planning (MRP) systems are two common systems with which the MBOM shares information.
Bill of Materials Examples
Flow charts and tables are popular formats to represent BOMs. It requires only little industry expertise to draft a BOM.
You should comprehensively understand the final product or entire project.
We’ll use the production of motorbikes for illustration.
Assume that you must produce 200 motorbikes. What components, parts, assemblies, and sub-assemblies will be required?
Example-1: Basic BOM (Flow Chart Method)
A basic BOM is illustrated in the flow chart below.
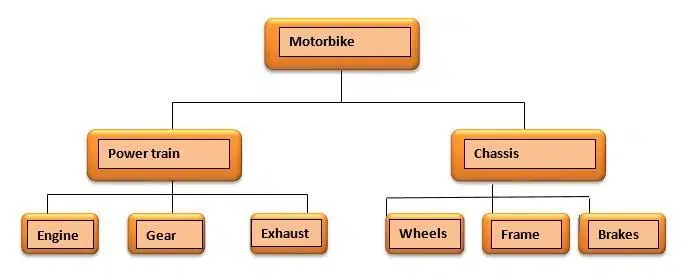
Example-2: Detailed BOM (Tabular Format)
As the name suggests, this format is more detailed and includes quantity, parts, part numbers, and the cost per unit of measurement.
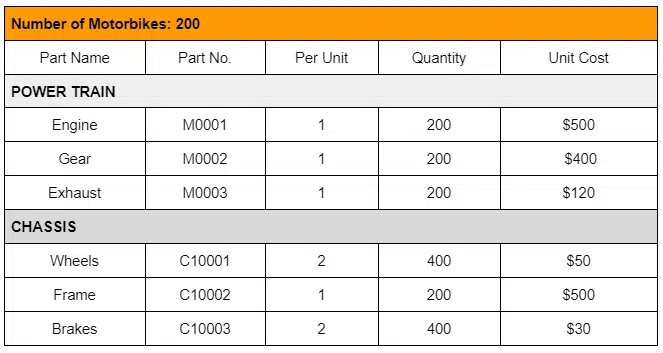
Advantages of the Bills of Materials
BOMs reduce manufacturing delays and inaccurate inventory counts, both of which can cost time and money. Other key advantages of BOM include:
- Provides Homogeneity: The goods stay consistent when every production run follows the same BOM.
- Monitoring Product Failures: The BOM data is crucial in monitoring product failure. You can pinpoint probable failure points and identify the parts, materials, and components that caused the failure.
- Makes Manufacturing More Effective: By determining the costs of each part required to produce a product, an organization may assess how it can proceed with production with the least number of risks. This reduces the possibility of both resource shortages and component overproduction.
- Control Costs and Schedule: BOMs assist manufacturers in staying within budget and on schedule by ensuring that the proper components and materials are available at the right time and in the right amounts.
Conclusion
A bill of materials (BOM) outlines the materials and parts needed in the production of the product or required in a project. It aids businesses in planning material purchases, estimating costs, planning and controlling inventories, as well as reducing manufacturing waste and delays.
A precise, comprehensive BOM makes it easier to pinpoint the root cause of a product failure and makes it possible to move rapidly to replace faulty materials, parts, and components.

I am Mohammad Fahad Usmani, B.E. PMP, PMI-RMP. I have been blogging on project management topics since 2011. To date, thousands of professionals have passed the PMP exam using my resources.